Does Stainless Steel Rust ?
When talking of stainless steel, it always refers to austenitic stainless steel (300 Series Stainless Steel), which includes 304, 316L, 321 and so on. As a professional stainless steel pipe supplier, it has always been asked whether the stainless steel can rust ? Here is the answer:
Stainless Steel Can Rust
Stainless steel will get rusted, and it will form a kind of oxide on the surface. Currently, the stainless steel sold in the market contains the element Cr, which can prevent the steel from being rusted. And the mechanism of corrosion resistance on stainless steel is the passivation film theory.
The so-called passivation film is a thin film with Cr2O3. This film can prevent the stainless steel from corrosion in varieties of media, which is called passivation.
About The Passivation Film
There are two reasons for the passivation: one is that the stainless steel itself has the ability of self-passivation, and this ability will be stronger with the increasement of the chromium content, making it become rust-resistant.
The another reason is the stainless steel forms a film during the corrosion when putting into aqueous solutions (electrolytes) – that’s why we need to do pickling and passivating for stainless steel pipe and fittings. Therefore, when the film is damaged, it will form a new passivation film immediately.
Why The Film Can Anti-Rusted ?
There are three reasons for the corrosion resistance on stainless steel: a) The film is extremely thin, and it is only a few microns even the chromium content exceeds 10.5%; b) The specific density of the passivation film is greater than the one of the matrixes.
Thus, it is difficult for the corrosive media to break the passivation film and further corrode the substrate; c) The chromium content is three times higher in the passivation film than the substrate, making it become highly resistant in corrosion.
Stainless Steel Can Be Corroded
Under certain circumstances, stainless steel will be corroded.
Due to its complicated application environment, the simple chromium oxide passivation film cannot meet the needs of highly corrosion-resistant environment. Therefore, according to the its different application, it requires the additional elements like molybdenum (Mo), copper (Cu), nitrogen (N) and others in the steel to improve the structure of the passivation film, making its corrosion resistance perform better.
If Mo is added, it will promote the collective passivation, and prevent the corrosion.
If Cu is added, the formation of Cucl will not interact with the corrosive medium, so that the improvement of its corrosion resistance can be achieved.
If N is added, the enrichment of Cr2N in the passivation film and the increase of Cr concentration in the passivation film will also intensify the corrosion resistance of steel.
The Corrosion-Resistance Performance
For the performance for SS corrosion resistance, there are some requirements. For example, 304 stainless steel may performs corrosion-resistant in a medium, but it may be destroyed in another media. Meanwhile, the corrosion resistance of stainless steel is relative. So far, no stainless steel can be corroded in all environments.
As shown in the picture on the right, due to the smoke dust falling on the surface of the stainless steel pipe, after a period of time in the open air and rain erosion, we can see that the rust spots has appeared in the stainless steel pipe surface . The distribution of rust spots is the location of the dusts.
Therefore, when corrosive substances adhere to the surface of stainless steel – such as iron filings, soot and similar stains, we should clean them up in time.
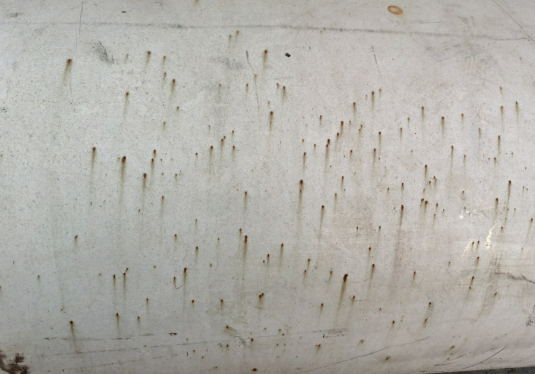
Sensitization of Stainless Steel
For stainless steel containing Cr, its surface will form a chromium oxide film and lose the chemical activity, which is called passivation state. However, if the austenitic system is under the temperature exceeding 475 to 850℃, element C will combine with element Cr, generating chromium carbide (Cr23C6) precipitation in the crystal boundary, so that the content of Cr near the grain boundary will be greatly reduced.
At this time, the corrosion resistance of steel will be reduced, and it will be very sensitive to the corrosive environment. This phenomenon is called sensitization. Sensitization is the most vulnerable to oxidized acid environments as well as welding heat affected areas and inter-thermal bending processing areas. The methods to prevent sensitization include:
- When the temperature rises or falls between 475~850℃, passing quickly to prevent element Cr combining with element C, so that chromium carbide cannot be precipitated.
- For the stainless steel which already occurs the sensitization phenomenon, please take high temperature solid solution treatment, and heating to the enough temperature to make chromium carbide decomposition (around 1040~1150℃). Then adopting rapid cooling, so that chromium carbide precipitation will not be able to precipitate.
- Adding low carbon stainless steel to 304L, 304LN, 316LN, 316LN, 316J1L, 317L, 317LN, so that element Cr cannot be combined with element C. Generally, when the content of C is below 0.05%, there will be no grain boundary corrosion in welding. However, special attention must be paid to the cleaning, and trying to avoid the pollution of oil and other substances containing C. When used in concentrated hot nitric acid or mixed acid containing hydroxy acid, the content of C should be less than 0.03%.
- Use stabilized stainless steel containing titanium (Ti) or niobium (Nb), such as 316Ti, 321, 347, 348. The affinity of Ti, Nb and C is greater than Cr, and the precipitation temperature of titanium carbide and niobium carbide is higher than chromium carbide, so that the precipitation of chromium carbide can be avoided.
In sum, the stainless steel can be rusted. But under the same environment, its corrosion rate is much lower than other steel, sometimes it even can be ignored.