September 2020 is the 90th anniversary history of duplex stainless steel
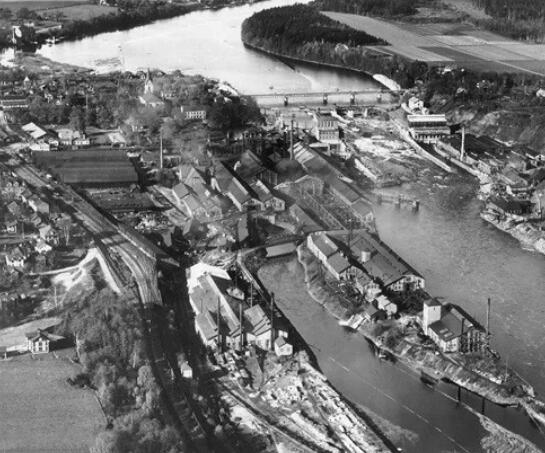
1930s to 1970s
In the early 1900s history of duplex stainless steel, the earliest stainless steels were pure austenite, ferrite or martensite. In 1930, Sweden’s Avesta Ironworks developed the first duplex stainless steel with a combination of ferrite and austenite.
In the early days, dual-phase steel was used for castings, bars and plates for pulping, papermaking and high-temperature applications due to its good corrosion resistance and castability. By 1932, duplex steel accounted for 6.5% of the global 5,500-ton global stainless steel market.
In the following decades, metallurgists developed techniques to reduce carbon content and introduce nitrogen to control plasticity and weldability. Improvements in the 1950s included the development of nitrogen-added duplex steel grades to reduce the risk of cracking during casting and welding.
Second-generation duplex stainless steel
The development of duplex steel reached its peak in the 1970s. The second-generation duplex stainless steel has better resistance to intergranular corrosion, and has gained more applications and greater commercial success.
From a metallurgical point of view, these steel grades utilize increased nitrogen to enhance the formation of austenite. This can prevent the duplex structure from reducing to full ferrite in the heat-affected zone after welding or hot working. Nitrogen also helps steel to resist pitting corrosion and at the same time increase strength.
3rd: Super Duplex
The development in the 1970s and 1980s was mainly the third generation of duplex steels: Forta SDX 2507, Forta SDX 100, the more highly alloyed super duplex stainless steels. These grades contain more alloying elements and therefore have better performance, but at a higher cost. Super duplex stainless steel meets the needs of the offshore oil, gas, food and beverage, and chemical industries.
The most common definition of super duplex stainless steel is that its pitting corrosion resistance (PRE or PREN) should reach at least 40. To achieve this level of corrosion resistance, metallurgists use alloying elements such as chromium, molybdenum, tungsten, nickel, and copper. Of course, more alloying elements in super duplex steels also mean higher costs, but compared with austenitic steels, they are usually more competitive in price and can be regarded as a substitute for austenitic steels .
Low Alloy Duplex Steel (Lean Duplex)
At the other end of the duplex steel product line, the Avesta plant developed low-alloy duplex stainless steel (Lean Duplex) in the mid-1980s to minimize raw material costs.
This is especially true when nickel is used as an alloying element. Over the years, the price of nickel has fluctuated sharply. Therefore, by reducing the nickel content, the stainless steel pipe fittings supplier can provide customers with more stable stainless steel products.
Among these Lean Duplex, Forta LDX 2101 is especially popular. It has higher manganese and nitrogen to compensate for its lower nickel content. It has high strength, good corrosion resistance and welding performance.
Formable Duplex
In the past 10-15 years, Duplex steel with improved molding properties has been further developed. The emergence of Formable Duplex Forta FDX 27 solves the problem that other duplex steels cannot have ductility and high strength at the same time, and cannot produce complex and lightweight molded parts.