Alliages à base de nickel sont une classe d'alliages qui présentent une grande solidité et un certain degré de résistance à l'oxydation et à la corrosion à des températures élevées de 650-1000℃.
Classification | Principaux types |
---|---|
Par performance principale (à base de nickel) | Alliage résistant à la chaleur |
Alliage résistant à la corrosion | |
Alliage résistant à l'usure | |
Alliage de précision | |
Alliage à mémoire de forme | |
Par Matrix Material | Superalliage à base de fer |
Superalliage à base de nickel | |
Superalliage à base de cobalt |
Rôle des principaux éléments des alliages à base de nickel
Lorsqu'il s'agit d'alliages à base de nickel, il faut d'abord parler de l'élément nickel.
Comme le fer et le cuivre, le nickel est utilisé dans les alliages depuis l'aube de la civilisation. Mais par rapport à l'acier, au laiton et au bronze, les alliages de nickel sont apparus tardivement dans l'industrie chimique. Les progrès constants de la métallurgie et de la technologie de fabrication ont favorisé le développement des alliages de nickel et facilité leur utilisation dans l'industrie chimique. Les alliages de nickel présentent une excellente résistance à la corrosion, une résistance mécanique, une ténacité, une stabilité métallurgique, une facilité d'usinage et de soudage. De nombreux alliages de nickel présentent également une excellente résistance à la chaleur, ce qui les rend idéaux pour les applications nécessitant une résistance à haute température et une résistance chimique à des températures élevées.
Le rôle principal du nickel dans les alliages à base de nickel est de modifier la structure cristalline du matériau. Une valeur importante du nickel dans les alliages à base de nickel est la formation d'une structure cristalline austénitique, qui améliore notamment la malléabilité, la soudabilité et la ténacité.
Les rôles des divers éléments autres que le nickel dans les alliages à base de nickel sont les suivants.
Abaissement du point de fusion de l'alliage, élargissement de la zone de température de la ligne de phase solide-liquide et formation de cristaux eutectiques à bas point de fusion. Effet désoxydant et réducteur et fonction de scorification. Durcissement et renforcement du revêtement. Amélioration des performances du processus d'exploitation.
Améliorer la résistance à la corrosion des acides non oxydants.
Effet de renforcement de la solution solide, effet de passivation. Amélioration de la résistance à la corrosion et de la résistance à l'oxydation à haute température. Formation d'une phase dure de carbure de chrome, de borure de chrome pour améliorer la dureté de l'alliage et la résistance à l'usure.
La solution solide provoque d'importantes distorsions du réseau, ce qui renforce considérablement la matrice de l'alliage. Améliorer la résistance à haute température et la dureté au rouge de la matrice. Peut couper et réduire l'organisation de la réticulation dans le revêtement. Améliorer la résistance à la cavitation et à l'érosion. Alliages de précision à base de nickel.
Représentant des alliages de nickel
Le premier alliage de nickel d'importance commerciale a été Alliage 400. Il a été développé et commercialisé en 1905 par l'International Nickel Company (Inco Alloys) sous la marque MONEL.
Les étapes suivantes ont été les suivantes alliage de nickel-molybdène B et le alliage de nickel-chrome-molybdène-tungstène Cqui ont été introduites vers 1930. Leur inventeur était la Haynes Stellite Company (Haynes International). Deux d'entre eux sont enregistrés sous la marque HASTELLOY.
L'étape suivante dans le développement des alliages à base de nickel a été franchie par Inco. Le développement d'alliages à base de alliage de nickel-chrome-fer 600 en 1931 et alliage nickel-fer-chrome en 1949 ont été nommés INCONEL et INCOLOY, respectivement.
Inco et Haynes ont capitalisé sur la popularité et la réputation de ces marques initiales pour introduire un total d'environ 50 alliages résistants à la corrosion et à la chaleur.VDM a développé et produit plus tard et de façon plus connue des alliages à base de nickel sous les marques Nicrofer, Nimofer et Nicorros.
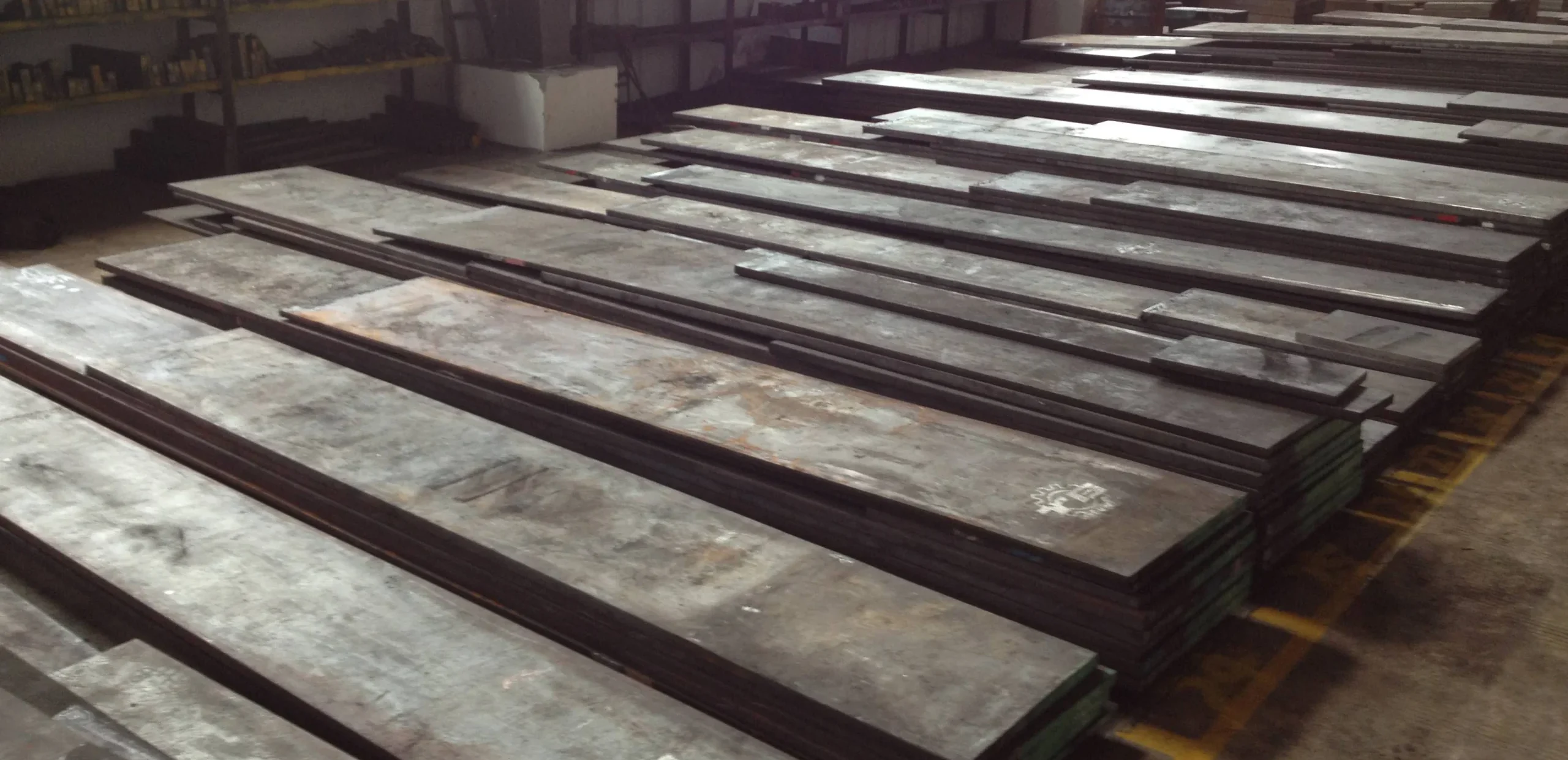
L'histoire
Nickel-based alloys were developed in the late 1930’s. Nimonic 75 (Ni-20Cr-0.4Ti) was first produced in the UK in 1941, and Nimonic 80 (Ni-20Cr-2.5Ti-1.3Al) was developed to improve creep strength and add aluminum. Nickel-based alloys were also developed in the USA in the mid-1940s, in the USSR in the late 1940s, and in China in the mid-1950s.
Son développement a inclus des améliorations dans la composition des alliages et des innovations dans les processus de production.
Au début des années 1950, le développement de la technologie de fusion sous vide a créé les conditions nécessaires à l'affinage des alliages à base de nickel contenant des niveaux élevés d'aluminium et de titane.
À la fin des années 1950, les températures de fonctionnement plus élevées des aubes de turbine exigeaient des alliages plus résistants à haute température. Cependant, la haute résistance de l'alliage rend difficile, voire impossible, sa déformation. Le procédé de moulage à la cire perdue a donc été utilisé pour mettre au point une série d'alliages de moulage présentant une bonne résistance à haute température.
Au milieu des années 60, le développement d'une série d'alliages de fonderie présentant une bonne résistance à haute température.
Au milieu des années 60, des alliages monocristallins à haute température et des alliages à haute température obtenus par métallurgie des poudres et présentant de bonnes performances ont été mis au point. Pour répondre aux besoins des navires et des turbines à gaz industrielles, un certain nombre d'alliages à base de chrome-nickel à haute teneur en chrome et en nickel ont également été mis au point depuis les années 1960, pour leur résistance à la chaleur et à la corrosion et leur bonne stabilité organisationnelle.
Du début des années 1940 à la fin des années 1970, soit environ 40 ans, la température de travail des alliages à base de nickel est passée de 700 ℃ à 1100 ℃, soit une augmentation annuelle moyenne d'environ 10 ℃.
Alliages de nickel Produit
Composition et propriétés
Les alliages à haute température à base de nickel sont les plus utilisés. Les principales raisons sont les suivantes : premièrement, ils peuvent dissoudre davantage d'éléments d'alliage et conserver une bonne stabilité organisationnelle. Deuxièmement, le composé intermétallique de type A3B ordonné en réseau co-lattice γ[Ni3(Al, Ti)] se forme en tant que phase de renforcement et renforce l'alliage. Enfin, des résistances à haute température plus élevées que celles des alliages à haute température à base de fer et des alliages à haute température à base de cobalt peuvent également être obtenues. Troisièmement, par rapport aux alliages haute température à base de fer, les alliages à base de nickel contenant du chrome présentent une meilleure résistance à l'oxydation et à la corrosion gazeuse.
Il contient plus d'une douzaine d'éléments, dont le chrome qui joue principalement le rôle d'antioxydant et de résistance à la corrosion. Il existe des éléments de renforcement en solution solide, des éléments de renforcement par précipitation et des éléments de renforcement des joints de grains en fonction de leurs effets de renforcement.
Selon la méthode de renforcement, on distingue les alliages de renforcement par solution solide et les alliages de renforcement par précipitation.
Processus de production
La fusion permet d'obtenir un acier plus purifié, de réduire la teneur en gaz et en éléments nocifs, mais en même temps, en raison de la présence d'éléments oxydables tels que Al, Ti, etc. dans certains alliages, il est difficile de contrôler l'existence d'une fusion sans vide. Même avec la fusion par induction sous vide et le four à autoconsommation sous vide ou le mode de refusion par four à laitier électroconducteur pour la production.
La déformation du forgeage, le processus de laminage, pour une mauvaise thermoplasticité de l'alliage et même l'utilisation de l'extrusion de billettes ouvertes après le laminage ou l'acier doux (ou l'acier inoxydable) veste processus d'extrusion directe. Le but de la déformation est de briser l'organisation de la coulée, d'optimiser la microstructure.
La coulée se fait généralement par fusion de l'alliage principal dans un four à induction sous vide afin de garantir la composition et de contrôler la teneur en gaz et en impuretés. Les pièces sont ensuite fabriquées par refonte sous vide - moulage de précision.
Dans le cas de l'alliage Udmet 500, par exemple, le système de traitement thermique comporte quatre étapes. Traitement de mise en solution, 1175°C, 2 heures, refroidissement à l'air. Traitement intermédiaire, 1080°C, 4 heures, refroidissement à l'air. Traitement de vieillissement primaire, 843°C, 24 heures, refroidissement à l'air. Traitement de vieillissement secondaire, 760°C, 16 heures, refroidissement à l'air. Afin d'obtenir l'état d'organisation requis et de bonnes performances globales.
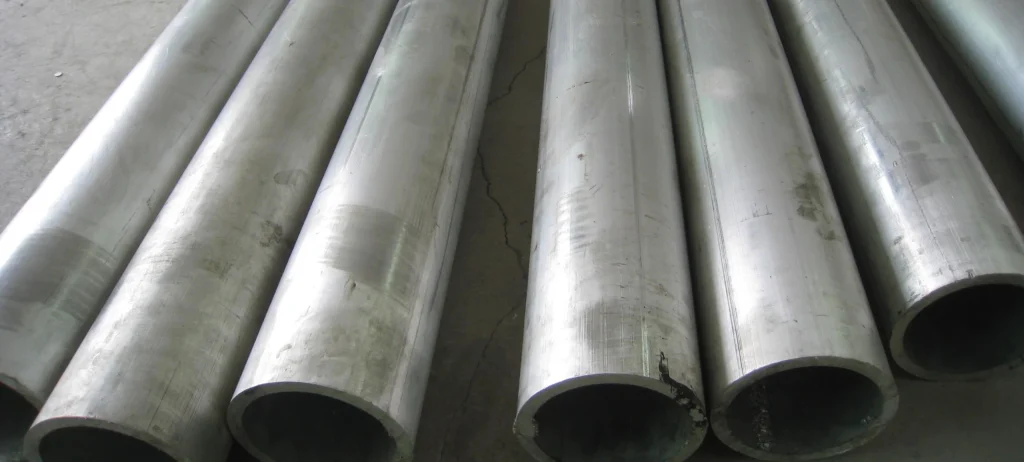
Alliages résistants à la corrosion à base de nickel
Les principaux éléments d'alliage sont le cuivre, le chrome et l'aluminium. molybdène. Il présente de bonnes performances globales et peut résister à la corrosion acide et à la corrosion sous contrainte. Les premières applications ont été les alliages nickel-cuivre, également connus sous le nom d'alliages monel. Il existe également des alliages nickel-chrome, des alliages nickel-molybdène, des alliages nickel-chrome-molybdène et des alliages nickel-chrome-molybdène. Les alliages résistants à la corrosion à base de nickel sont indispensables à la fabrication de pièces environnementales résistantes à la corrosion dans les secteurs du pétrole, de la chimie, de l'énergie électrique et autres.
Catégorie
L'alliage Ni-Cu présente une meilleure résistance à la corrosion que le nickel en milieu réducteur et une meilleure résistance à la corrosion que le cuivre en milieu oxydant. C'est le meilleur matériau pour résister aux températures élevées du gaz fluor, du fluorure d'hydrogène et de l'acide fluorhydrique en l'absence d'oxygène et d'oxydant.
Alliage Ni-Cr Également connu sous le nom d'alliage résistant à la chaleur à base de nickel, il est principalement utilisé dans des conditions de milieu oxydant. Résistant à l'oxydation à haute température et à la corrosion des gaz contenant du soufre et du vanadium, leur résistance à la corrosion augmente avec la teneur en chrome. Ces alliages présentent également une bonne résistance à la corrosion par les hydroxydes (tels que NaOH, KOH) et une bonne résistance à la corrosion sous contrainte.
Les alliages nickel-molybdène sont principalement utilisés dans des conditions corrosives en milieu réducteur. C'est l'un des alliages qui présente la meilleure résistance à la corrosion à l'acide chlorhydrique. Cependant, en présence d'oxygène et d'agents oxydants, sa résistance à la corrosion est fortement réduite.
L'alliage Ni-Cr-Mo (W) présente les mêmes performances que l'alliage Ni-Cr et l'alliage Ni-Mo ci-dessus. Principalement utilisé dans des conditions de milieu mixte oxydant-réducteur. Ce type d'alliage présente une bonne résistance à la corrosion dans le gaz de fluorure d'hydrogène à haute température, dans l'oxygène et l'agent oxydant contenant de l'acide chlorhydrique, dans la solution d'acide fluorhydrique, ainsi qu'à température ambiante dans le gaz de chlore humide.
Les alliages Ni-Cr-Mo-Cu sont résistants à la corrosion par l'acide nitrique et l'acide sulfurique et présentent une bonne résistance à la corrosion dans certains acides mixtes d'oxydoréduction.
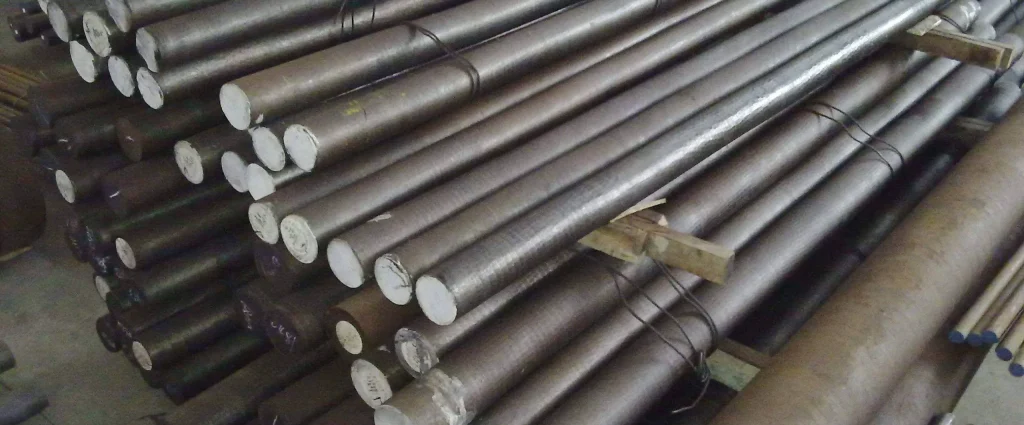
Alliages résistants à l'usure à base de nickel
Les principaux éléments d'alliage sont le chrome, le molybdène, le tungstène, et contiennent également une petite quantité de niobium, de tantale et d'indium. Outre la résistance à l'usure, la résistance à l'oxydation, la résistance à la corrosion et les performances de soudage sont également bonnes. Il permet de fabriquer des pièces résistantes à l'usure. Il s'agit également d'un matériau de revêtement, qui agit comme une couche sur d'autres surfaces de substrat par le biais du processus de revêtement et de pulvérisation.
Il existe principalement des poudres d'alliage autofondantes et des poudres d'alliage non autofondantes.
La poudre de nickel non autofusible est une poudre d'alliage à base de nickel sans B, Si ou avec une faible teneur en B, Si. Ce type de poudre est largement utilisé dans le revêtement par projection d'arc plasma, le revêtement par projection de flamme et le renforcement de la surface par plasma. Il s'agit principalement des poudres suivantes la poudre d'alliage Ni-Cr, la poudre d'alliage Ni-Cr-Mo, la poudre d'alliage Ni-Cr-Fe, la poudre d'alliage Ni-Cu, la poudre d'alliage Ni-P et Ni-Cr-P, la poudre d'alliage Ni-Cr-Mo-Fe, la poudre d'alliage Ni-Cr-Mo-Si à haute résistance à l'abrasion, la poudre d'alliage Ni-Cr-Fe-Al, la poudre d'alliage Ni-Cr-Fe-Al-B-Si, la poudre d'alliage Ni-Cr-Si, la poudre d'alliage résistant à l'usure et à la corrosion à base de Ni-Cr-W, et ainsi de suite.
L'ajout de quantités appropriées de B et de Si aux poudres d'alliage de nickel entraîne la formation de poudres d'alliage autofusibles. La poudre d'alliage autofusible, également connue sous le nom d'alliage à bas eutectique et d'alliage de rechargement, est constituée d'alliages à base de nickel, de cobalt et de fer auxquels on ajoute des éléments d'alliage eutectiques à bas point de fusion (principalement du bore et du silicium) pour former une série de matériaux en poudre. Les produits les plus couramment utilisés sont la poudre d'alliage Ni-B-Si, la poudre d'alliage Ni-Cr-B-Si, Ni-Cr-B-Si-Mo, Ni-Cr-B-Si-Mo-Cu, la poudre d'alliage autofondant à base de Ni-Cr-W-C, la poudre d'alliage autofondant à haute teneur en cuivre, etc.
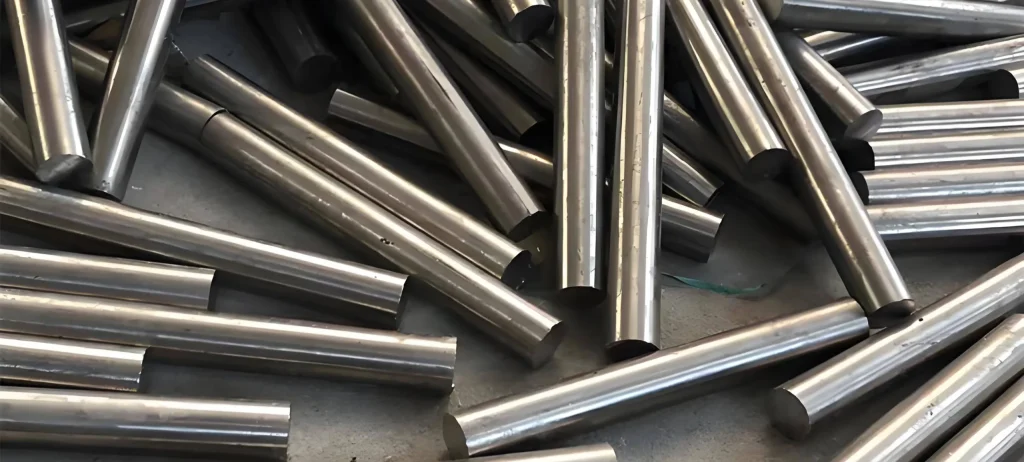
Alliages de précision à base de nickel
Il s'agit notamment d'alliages magnétiques doux, d'alliages de résistance de précision et d'alliages électrothermiques. Les alliages magnétiques doux les plus couramment utilisés sont les alliages Bomol contenant environ 80% de nickel, qui présentent une perméabilité maximale et une perméabilité de départ élevées, ainsi qu'une faible coercivité, et constituent des matériaux de base importants pour l'industrie électronique. Les principaux éléments d'alliage des alliages de résistance de précision sont le chrome, l'aluminium et le cuivre. Cet alliage présente une résistivité élevée, un faible coefficient de température de résistance et une bonne résistance à la corrosion. Il s'applique à la fabrication de résistances. L'alliage électrothermique est un alliage de nickel contenant du chrome 20%. Il présente une bonne résistance à l'oxydation et à la corrosion et peut être utilisé à long terme à une température de 1000 ~ 1100 ℃.
Alliages à mémoire de forme à base de nickel
Il contient du titane 50%. Sa température de récupération est de 70°C avec un bon effet de mémoire de forme. Une légère modification de la proportion de composants en nickel et en titane peut faire varier la température de récupération entre 30 et 100 ℃. Principalement utilisé dans la fabrication de vaisseaux spatiaux utilisés dans l'ouverture automatique des composants structurels, l'industrie aérospatiale, les fixations auto-excitées, l'utilisation biomédicale des moteurs de cœur artificiel et ainsi de suite.