Definición de aleaciones a base de níquel
Las aleaciones con un contenido de Ni superior a 30wt% se denominan aleaciones a base de níquel. Los productos comunes tienen un contenido de Ni superior a 50wt%. Debido a su superior resistencia mecánica a altas temperaturas y resistencia a la corrosión, se combinan con aleaciones a base de hierro y cobalto como superaleaciones (superaleación).
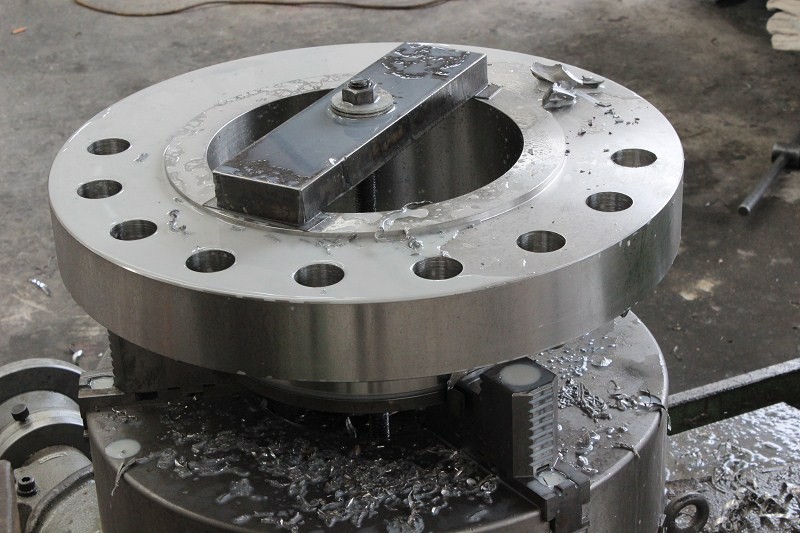
Este tipo de aleación se usa generalmente en un ambiente de alta temperatura por encima de 540 ℃, y se seleccionan diferentes aleaciones según la aplicación. Se utiliza principalmente en entornos especiales resistentes a la corrosión, entornos de corrosión de alta temperatura y equipos que requieren resistencia mecánica a altas temperaturas.
A menudo se utiliza en la industria aeroespacial, energética, petroquímica o en campos especiales de electrónica / optoelectrónica.
Campos de aplicación | Características de los requisitos | Uso del producto |
Aeroespacial | Mantenga una buena resistencia mecánica a temperaturas extremadamente altas. | Motores de aviones, turbinas de gas, válvulas de motor |
Energía | Buena resistencia a la vulcanización a alta temperatura y a la oxidación a alta temperatura | Piezas de hornos, aislamiento, industria de tratamiento térmico, industria de petróleo y gas |
Petroquímico | Resistente a la corrosión por solución acuosa (ácido, álcali, ion cloruro) | Planta desaladora, oleoducto petroquímico |
Electrónica | Entorno general con baja resistencia a la corrosión o resistencia a altas temperaturas | Piezas de la carcasa de la batería, marco de plomo, cubierta de red para monitor de computadora |
Origen y desarrollo
La aleación a base de níquel se desarrolló a fines de la década de 1930. La aleación a base de níquel Nimonic 75 (Ni-20Cr-0.4Ti) se produjo por primera vez en el Reino Unido en 1941. Para aumentar la resistencia a la fluencia, se agregó Al para desarrollar Nimonic 80 (Ni-20Cr-2.5 Ti-1.3Al ); mientras que Estados Unidos a mediados de la década de 1940, Rusia a fines de la década de 1940, China a mediados de la década de 1950 también desarrollaron aleaciones a base de níquel.
El desarrollo de aleaciones a base de níquel incluye dos aspectos, a saber, la mejora de la composición de las aleaciones y la innovación de la tecnología de producción.
Por ejemplo, a principios de la década de 1950, el desarrollo de la tecnología de fusión al vacío creó las condiciones para el refinado de aleaciones a base de níquel que contienen altos niveles de Al y Ti, e impulsó un aumento sustancial en la resistencia de la aleación y la temperatura de servicio. A finales de la década de 1950, debido al aumento de la temperatura de trabajo de las palas de las turbinas, se requería que las aleaciones tuvieran una mayor resistencia a altas temperaturas. Sin embargo, cuando la resistencia de la aleación era alta, era difícil o incluso imposible de deformar. Por lo tanto, se utilizó la tecnología de fundición de precisión para desarrollar una serie de resistencias a altas temperaturas. De aleaciones de fundición. A mediados de la década de 1960, se desarrollaron superaleaciones cristalinas y monocristalinas direccionales de mejor rendimiento y superaleaciones de pulvimetalurgia.
Para satisfacer las necesidades de los barcos y las turbinas de gas industriales, desde la década de 1960 se han desarrollado varias aleaciones a base de níquel con alto contenido de Cr con buena resistencia a la corrosión térmica y estructura estable. En aproximadamente 40 años, desde principios de la década de 1940 hasta finales de la de 1970, la temperatura de trabajo de las aleaciones a base de níquel aumentó de 700 a 1100 ° C, un aumento anual promedio de aproximadamente 10 ° C. Hoy en día, la temperatura de servicio de las aleaciones a base de níquel puede superar los 1.100 ℃. Desde la aleación Nimonic75 antes mencionada con una composición simple hasta la aleación MA6000 recientemente desarrollada, la resistencia a la tracción a 1100 ℃ puede alcanzar los 2220 MPa y el límite elástico es 192 MPa; Su durabilidad en condiciones de 1.100 ℃ / 137MPa es de aproximadamente 1.000 horas y se puede utilizar para palas de motores aeronáuticos.
Características de las aleaciones a base de níquel.
Las aleaciones a base de níquel son los materiales más resistentes y más utilizados en las superaleaciones. El nombre de la súper aleación se deriva de las características del material.
- (1) Excelente rendimiento: puede mantener una alta resistencia a altas temperaturas y tiene una excelente resistencia a la fluencia, resistencia a la fatiga y otras propiedades mecánicas, así como resistencia a la oxidación y corrosión, y buena plasticidad y soldabilidad.
- (2) La adición de aleaciones es muy complicada: las aleaciones a base de Ni a menudo agregan más de diez elementos de aleación para mejorar la resistencia a la corrosión de diferentes entornos; y fortalecimiento de la solución sólida o fortalecimiento de la precipitación.
- (3) El entorno de trabajo es extremadamente severo: las aleaciones a base de níquel se utilizan ampliamente en diversas condiciones de funcionamiento adversas, como piezas de alta temperatura y alta presión de cámaras de gas de motores de vuelo aeroespaciales, piezas estructurales para energía nuclear, petróleo, industrias marinas y Tuberías resistentes a la corrosión.
El efecto de varios elementos en
El níquel metálico retiene la austenita y una estructura cúbica centrada en las caras hasta que alcanza su punto de fusión. Esto proporciona un grado de libertad para la transición dúctil-frágil y también reduce en gran medida los problemas de fabricación causados por la coexistencia de otros metales. En la secuencia electroquímica, el níquel es inerte que el hierro y más activo que el cobre. Por lo tanto, en un entorno reductor, el níquel es más resistente a la corrosión que el hierro, pero no el cobre. Sobre la base de níquel y cromo, la aleación tiene resistencia a la oxidación, lo que puede producir muchos tipos de aleaciones con una gama muy amplia de aplicaciones, de modo que puedan tener la mejor resistencia a entornos reductores y oxidantes.
En comparación con el acero inoxidable y otras aleaciones a base de hierro, las aleaciones a base de níquel pueden contener más elementos de aleación en un estado de solución sólida y pueden mantener una buena estabilidad metalúrgica. Estos factores permiten la adición de una variedad de elementos de aleación, de modo que se puede utilizar una gran cantidad de aleaciones a base de níquel en diversos entornos corrosivos.
Los elementos comunes en las aleaciones a base de níquel incluyen principalmente:
Níquel:
Proporciona estabilidad metalúrgica, mejora la estabilidad térmica y la soldabilidad, mejora la resistencia a la corrosión para reducir los ácidos y la sosa cáustica y mejora la resistencia al agrietamiento por corrosión bajo tensión, especialmente en entornos de cloruro y sosa cáustica.
Cromo:
Mejora las propiedades anti-oxidación y anti-oxidación a alta temperatura, anti-azufre y mejora las propiedades anti-picaduras y corrosión por grietas.
Molibdeno:
Mejore la resistencia a la corrosión de los ácidos reductores, mejore la resistencia a la corrosión por picaduras y grietas en el entorno de solución acuosa que contiene cloruro y mejore la resistencia a altas temperaturas.
Planchar:
Mejore la resistencia al ambiente de carburación de alta temperatura, reduzca el costo de la aleación y controle la expansión térmica.
Cobre:
Mejorar la resistencia a la corrosión de los ácidos reductores (especialmente los ácidos sulfúrico y fluorhídrico utilizados en lugares donde el aire no circula) y sales. La adición de cobre a la aleación de níquel-cromo-molibdeno-hierro ayuda a mejorar la resistencia al ácido fluorhídrico, la resistencia a la corrosión del ácido fosfórico y el ácido sulfúrico.
Aluminio:
Mejora la resistencia a la oxidación a altas temperaturas y el endurecimiento por envejecimiento.
Titanio:
Combinado con el carbono, reduce la corrosión intergranular causada por la precipitación del carburo de cromo durante el tratamiento térmico y mejora el fortalecimiento del envejecimiento.
Niobio:
Combinado con el carbono, reduce la corrosión intergranular causada por la precipitación del carburo de cromo durante el tratamiento térmico, mejora la resistencia a la corrosión por picaduras y grietas y mejora la resistencia a altas temperaturas.
Tungsten:
Mejore la resistencia para reducir la corrosión ácida y local, mejore la resistencia y la soldabilidad.
Nitrógeno:
Mejore la estabilidad metalúrgica, mejore la resistencia a la corrosión por picaduras y grietas y aumente la resistencia.
Cobalto:
Proporciona mayor resistencia a altas temperaturas, mayor resistencia a la carbonatación y vulcanización.
Muchos de estos elementos de aleación pueden combinarse con níquel en una amplia gama de composiciones para formar una solución sólida de una sola fase, asegurando que la aleación tenga una buena resistencia a la corrosión en muchas condiciones corrosivas. La aleación también tiene buenas propiedades mecánicas en un estado completamente recocido, sin preocuparse por los cambios metalúrgicos dañinos causados por la fabricación o el procesamiento térmico. Muchas aleaciones con alto contenido de níquel pueden aumentar su resistencia mediante el endurecimiento de la solución sólida, la precipitación de carburo, el endurecimiento por precipitación (envejecimiento) y el reforzamiento de la dispersión.
publicado por accesorios de tubería de acero inoxidable kaysuns